Brief History
Originally founded in 1844 by Linus Yale Jr. with his invention of the pin-tumbler cylinder lock, the company evolved into Yale and Towne manufacturing co. in 1868 through Yale’s partnership with Henry Towne.
1875 saw the company expand its product offering from just locks to also include materials handling. in 1920 the company released a battery powered low-lift platform truck, followed by a range of high-lift platform trucks, tow tractors and one of the first lift trucks with tilting forks.
Over 137 years later these high quality units still underpin the current range of industry leading materials handling forklifts and equipment engineered and manufactured by Yale.
The 1930’s saw the Yale brand grow internationally with manufacturing operations opened in England U.K., Germany and Japan through sales and acquisition of existing forklift companies.
1950 saw Yale add gas, LPG and diesel powered forklifts trucks to its ever expanding range of products.
Throughout the 1960’s and 70’s the company continued to grow and prosper through a merger with multinational Eaton Corp and later due to forklifts being manufactured in Japan under license through an exclusive partnership with Sumitomo Ltd which lead to the creation of the joint venture company Sumitomo Yale Co. Ltd.
1985 saw the company being to resemble the materials handling leader it is today as Yale Materials Handling Corporation was formed following the company’s acquisition by North American Coal Corporation, later named NACCO Industries inc.
The 1990’s saw the company continue to grow into the large multinational MHE supplier it is today with further expansion into the UK acknowledged with the Queen award in 1990 for export achievement.
1992 saw the creation of Yale Europe Materials Handling to market Yale branded materials handling forklifts and units to the wider European, African and Middle East markets.
In 2012 Hyster-Yale Materials Handling Inc. was formed as a spin off from NACCO Industries Inc. and today is still the parent company for both industry leading brands Yale and Hyster forklifts.
Yale Brand Today
Today the Yale brand is synonymous with high quality innovative materials handling forklifts and units, backed by the industry leading Hyster-Yale Materials Handling Inc.
Through its operating subsidiary NACCO Materials Handling Group (NMHG) Yale materials handling forklift, units and spare parts are designed, engineered, manufactured, sold and serviced globally.
NMHG is one of the top three global suppliers of materials handling forklifts with an estimated 785,000 units in operation and 5,000 strong workforce of employees globally.
With leadership and foresight provided by the wider NMHG, Yale continue to focus on key programmes based on:
- Innovation
- Quality and efficiency
- Sales and service excellence
- Global coverage
- Organisational excellence
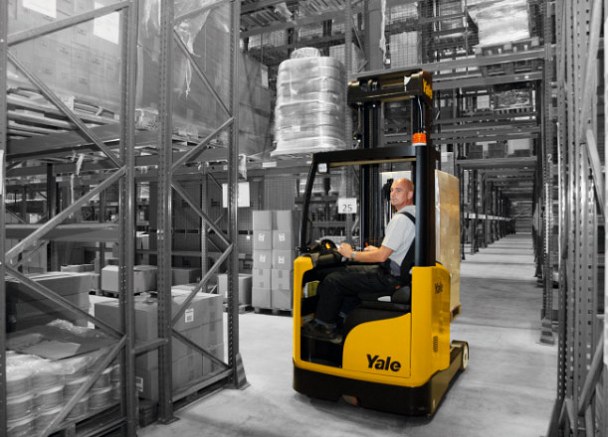