Cardboard boxes vs. Reusable plastic containers – Office Depot green solution
Cardboard boxes can become an expensive shipping expense for businesses that deliver high volumes of orders direct to customers. One solution is to remove the need for cardboard boxes and packaging materials and replace them with reusable plastic containers combined with light weight paper bags for final delivery. The plastic containers protect the goods held in the paper bag during shipping and transportation.
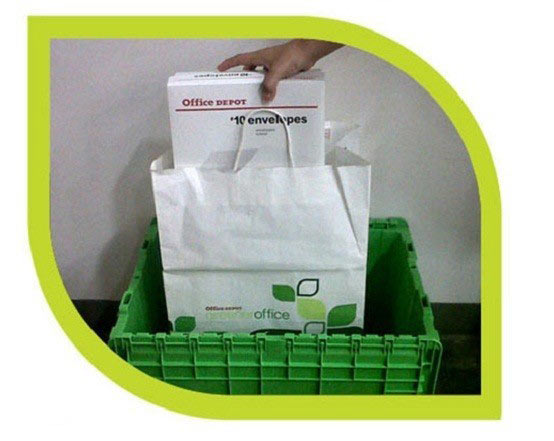
Office Depot has implemented this exact system. Office Depot is a major office supplier with sales of $11.5 Billion in 2011.
“Over the years, we’ve used millions of cardboard boxes and plastic air pillows for delivering our products. For orders delivered in bags, we will reduce the number of boxes used for deliveries and also eliminate the use of air pillows.”
“Office Depot bags contain 40% post-consumer recycled contact and plastic totes are made from 60% post-consumer recycled plastics.”
Using paper bags reduces overall materials helping to reduce wastage. Some people argue that cardboard boxes are recyclable and hence are not that bad for the environment, but cardboard can only be recycled a limited amount of times before the paper fibers become weak and unusable for cardboard or paper application. This system will help reduce tons of cardboard and packaging waste annually.
What’s the cost?
The real question managers are probably asking is how cost effective is it? To further investigate how cost effective this type of solution is I’ve done some calculations.
The pricing for the calculations below were taken from some major suppliers of packaging in Australia. I would recommend adding your own quotes and figures into my calculation to see how cost effective this solution is for your business.
Key Factors to consider before implementation:
- Cost of Cardboard boxes
- Cost of padding (bubble wrap, air pillows etc.)
- Cost of Paper bags.
- Cost of reusable containers (calculate initial cost, then add a percentage of stock loss)
- Labour of handling and packaging. (Time packing and handling time for both solutions and see what’s more cost effective)
- Compare total weight of both packaging solutions (I haven’t included this in my calculations but it’s worth looking at, as the greater the weight the higher the fuel costs)
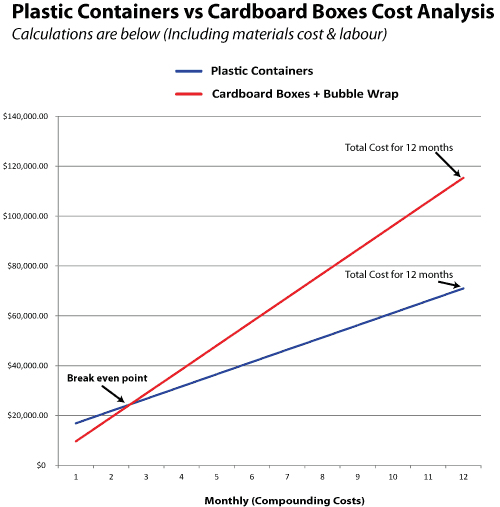
In the first month the initial cost of plastic containers is $16,855, while cardboard boxes are significantly lower at only $9,714 a difference of $7,142, but by half way through the second month plastic containers have already broken even with cardboard costs (As the ongoing cost is $4,693 less per month). These savings are based on lower labour costs and reduced materials costs.
After this point plastic containers provide significant savings. By month 12 there is a saving of $44,384 by selecting plastic containers (due to lower ongoing costs).
The above estimate is based on order quantities of 10,000 per month. In smaller volumes over shorter periods of time cardboard boxes are a lower cost solution.
Here are some of the calculations for the first month:
Let’s say that 10,000 orders were delivered in the 1st month. Let’s estimate we need 500 Plastic reusable containers for deliveries. This is based on the assumption that there are 334 deliveries per day, which would equal around 10,020 units per month. The extra 166 units are for stock loss and daily order variations.
- Plastic containers 45L: 500 units X $26.52 per units = $13,260 (Initial investment, damage to container and stock loss I’ve estimated at 10% which would equal an ongoing cost of $1,326)
- Paper Bags Large: 10,000 units X $0.304 per bag = $3,040
- Labour cost per order: 10 seconds which equals 27.78 Hours of Labour per 10,000 packages = $555.60 (At $20 per hour)
Estimated Labour times: Add item to paper bag 5 sec, close paper bag / seal 5 sec
Total Cost $16,856
Cardboard Boxes Solution
- Cardboard boxes 152×152×152: 5000 units X $0.48 per unit = $2500
- Cardboard boxes 203×203×203: 5000 units X $0.74 per unit = $3700
- Bubble wrap 20 cm per box: 10,000 units X $0.2126 = $2126
- Labour cost per order: 25 second which equals 69.44 Hours of Labour per 10,000 packages = $1388.8 (At $20 per hour)
Estimated Labour time: Building the boxes: 10 seconds, cutting the bubble wrap 5 sec, wrapping and packaging item 5 sec, tapping up the box 5 sec.
Total Cost $9,715
It looks like plastic reusable containers could be a great solution for businesses that deliver direct to their customers, with the opportunity to reduce waste and reduce costs.