Block Stacking – Warehouse Basics
One common method of storing stock is floor pallet stacking or block stacking. Block stacking is a form of palletised storage that does not require any type of storage equipment, and instead loaded pallets are placed directly on the floor and built up in stacks to a maximum stable storage height. Lanes are created to ensure access to the different stock keeping units (SKUs).
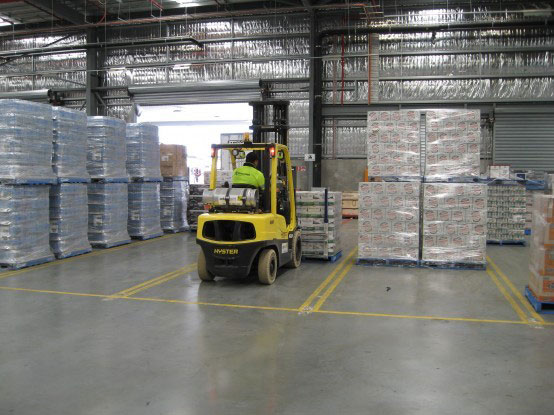
The maximum storage heights or stacking levels are determined by a number of different factors such as:
- Load strength (crushability)
- Load weight
- Load stability
- Pallet conditions
- Safety limits
- Weather (humidity, water, wind can weaken pallets and soften loads)
- Warehousing clearance heights
Each of these factors needs to be considered carefully to ensure that safe stacking levels are selected.
One key limitation of block stacking is that SKU’s are only accessible in a Last In First Out (LIFO) method. Floor stacking is extremely space intensive and hence requires very large areas for storing large quantities of stock.
When loads are removed from the storage lanes, underutilised space is created that cannot be used until the entire lane is cleared. This effect is called honeycombing. Therefore careful attention to lane length and depth (determine storage capacity) must be taken to ensure that a high level of utilisation of each line is achieved, meaning that each line size needs to be planned based on predicted and current stock output levels for each SKU.
If we look at the picture below we can see a classic example of floor stacking at a port in Melbourne. The Containers are stacked up to 7 containers in height; in this case they are restricted by safety & weather conditions and not load strength.
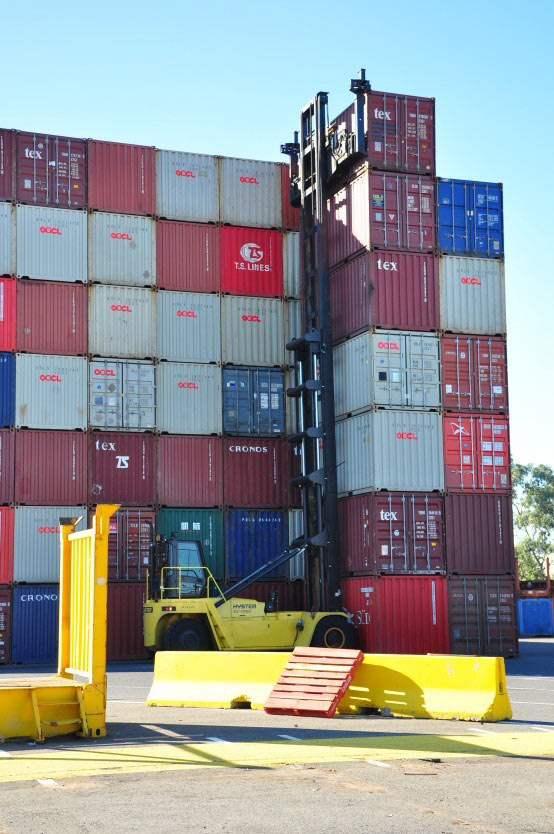
Advantages of floor stacking:
- Very low setup costs
- Flexible
Disadvantages of floor stacking:
- Low density storage (Requires a large storage facility to store only a small amount of stock).
- Poor ventilation of products
- Storage height depends on a number of variable factors
- Only one SKU can be effectively stored in a lane, empty pallet spaces are created that cannot be utilized effectively until an entire lane is emptied.
- You have to move the top pallet to get to the pallet underneath (LIFO)