Improving the Layout of your Warehouse
An inefficient layout of your warehouse can have a negative effect on your business. Decreasing productivity, creating inventory control issues, errors in shipping and posing safety risks. When it comes to laying out your warehouse, it is important to exploit its full space. Everything should be accessible and in the right location, allowing staff to carry out their duties in the most efficient way. Ensuring every square foot of space is properly utilised, within your warehouse, will keep overhead costs to a minimum and increase productivity.
Here are some useful tips to help plan the best warehouse layout.
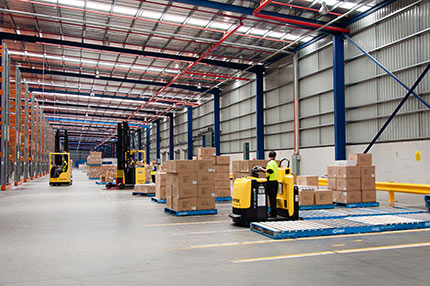
Super-size the Receiving Area:
Receiving is arguably the most critical function of the warehouse. It is important to ensure you have enough room for your staff to carry out all of the necessary activities from breaking down pallets to counting items. The more space there is in the receiving area, then the easier it is for your staff to complete the job efficiently.
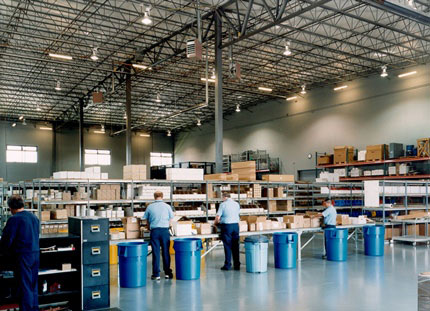
Segmentation:
Warehouse activity can be fast and dynamic which is why it is necessary to create segments in the warehouse that are well defined. For example, your returned products area should be in a separate part of your warehouse that is enclosed by a fence and clearly marked. This ensures that returned products are not mistaken for stock.
It is also important to keep shipping and receiving areas separate and located in different areas of the warehouse to avoid improper staging of freight merchandise.
Set up bin locations and pick path:
In order to provide your pickers with the best possible chance at filling their order right the first time, make sure they have adequate instructions. The pick path refers to the direction that you want your pickers to move down the aisle. It should start at the farthest point away from the shipping area and dump the picker in front of the shipping prep area.
Sketch out the pick paths on paper ahead of time. The idea is that pickers will make one pass through the facility in the most efficient way possible.
Inventory:
Design your warehouse so that inventory does not need to be moved more than once. It usually does not make sense to store items in one place and then move them to another place later.
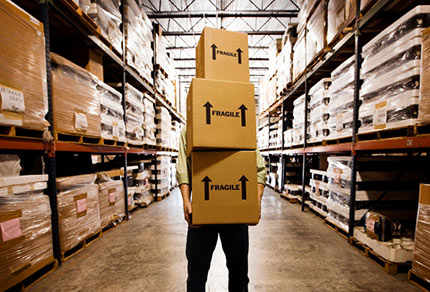
Special packaging area:
Certain products need a value add or special packaging area. This needs to be adjacent to the shipping area, because the product will move directly from the value add area to the shipping area. This area is difficult to cube out and takes up a lot of valuable warehouse space. Therefore, the value adds area should be kept as small as possible.
Random location strategy:
A random location strategy is the idea that a warehouse is laid out according to product accessibility other than popularity. This is because product popularity changes based upon buying cycles and company advertising. It is therefore best to arrange products in another manner.
As long as easy access to products is maintained, the random location strategy is generally one of the more effective ways to lay out a warehouse.
Aisles:
Ensure quick product availability by having a system of aisles and cross aisles that make it easier to move around your warehouse. Long and continuous aisles can make it difficult in getting from one part of the warehouse to another. However, cross aisles that allow access to the main aisles, help create a grid that is more efficient and easier to navigate.
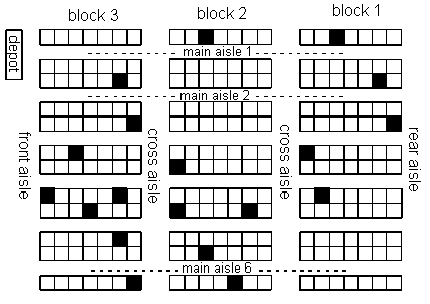
The goal of the warehouse layout is to optimise your warehousing functions and achieve maximum efficiency and space utilisations.