Combilift’s Covid-19 Operational and Manufacturing Changes
As many countries continue to be affected by the Covid-19 pandemic, whole manufacturing industries have been temporarily shut down to ensure the health and safety of all people.
Some countries that have not been severely impacted by Covid-19 or that have been able to flatten the viruses impact to allow manufacturing to resume such as Ireland, home of our supplier Combilift the global leader in the manufacturing of multi-directional forklifts.
Whilst manufacturing is able to resume it comes with a number of new restrictions and guidelines to safeguard the health of employees and the general public.
This week’s blog gives an insight into the changes Combilift has implemented to comply with Covid-19 restrictions and guidelines to safeguard their employees’ health, whilst allowing their manufacturing operations to continue.
Introduced Social Distancing Measures
All Combilift staff on site in offices and factories are observing social distancing guidelines, maintaining a minimum of 2m gap between themselves and any other employee.

To accommodate the 2m gap requirement office workspaces have been temporarily reorganised with only every second workspace being utilised.
Floor markings have also been laid out to assist employees in keeping a 2m gap between themselves at all times.
Out in the factory the manufacturing area has been reorganised with storage areas decreased in size to allow for the factory floor to be expanded.
The expanded factory floor has allowed for work stations and machinery to be spaced appropriately apart to allow employees working in these areas to comply with social distancing maintaining the 2m gap.
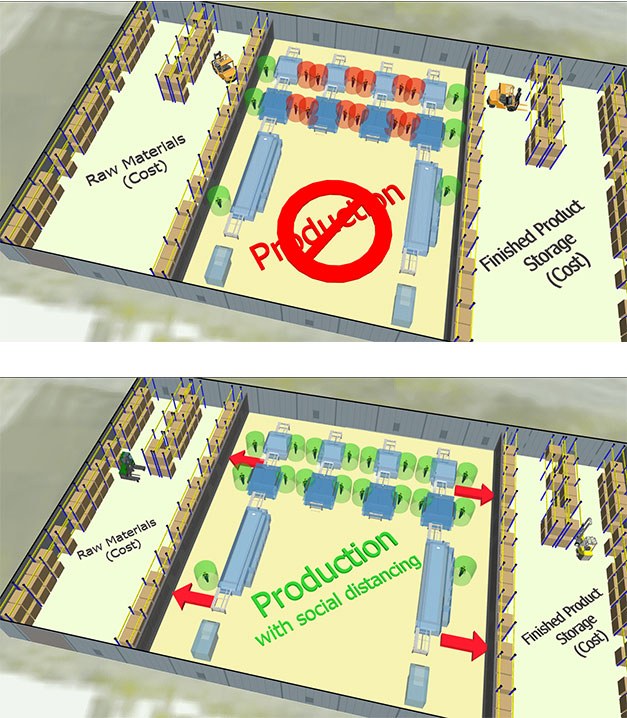
The factory is now divided into eight separate segments each with its own small canteen, whilst the company’s large canteen is closed to prevent employees congregating in the one area at meal times.
Increased Emphasis on Personal Hygiene
Combilift has encouraged all employees to be vigilant regarding their personal hygiene, particularly the regular washing of hands to prevent Covid-19 from spreading.
To assist staff Combilift has installed a number of hand sanitiser stations to dispense germ kills sanitiser as staff move throughout the facility.
Particular emphasis has been paid to high traffic areas such as facility entrances where staff are required to sanitise their hands before entry at all times.
Sanitiser has also been provided near to commonly touched objects such as time keeping swipe machines so staff can immediately sanitise their hands after touching the common object, normal swipe cards have also been replaced with wireless key fobs.
To assist employees where possible all door are left open so employees are not constantly touching door handles, doors that can’t be left open have had copper treatments applied to them which halves the time Covid-19 virus spores can stay alive on the surface compared to steel
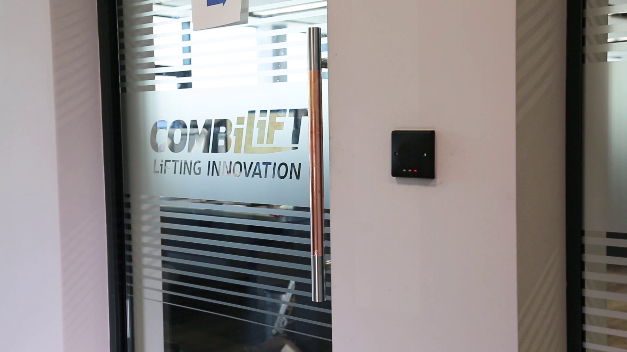
Wearing of Personal Protective Equipment
All Combilift employees are required to wear personal facemasks when working in offices and workshops.
The increased use of such as facemasks reduces the risk of spreading the virus from employee’s breathing, sneezing or coughing.
Employees are also required to wear disposable plastic gloves, providing protection when touching objects and surfaces.
The disposable gloves can be safely disposed of when they have completed a task or at the end of their shift in a bin and they can wear a new pair of gloves when they resume work.a
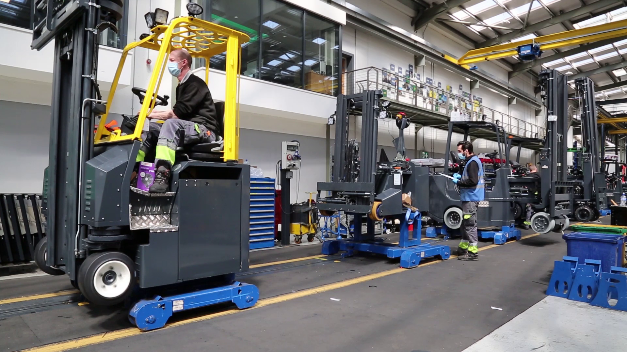
Employee Temperature Checks
A common symptom displayed by those affected by Covid-19 is fever indicated via a raised body temperature.
Combilift has implement thermal imaging temperature checks at all points of entry to its facilities.
This screens the temperature of all employees entering the building.
Completing this check at the buildings doors allows for a rapid response to any employee displaying a high temperature, they can be stopped immediately and sent for medical assessment or testing.
Being able to capture any employee with potential fever at the building door greatly reduces the risk of them passing on the virus as they haven’t been able to enter main areas of the building where other employees may already be working.
Shift Segregation
Combilift’s entire single shift operation manufacturing staff have temporarily been divided into two shifts resulting in a halving of total employees in the factory at any one time.
Each shift now means there are only ever a maximum of 350 employees in the company’s 46,500m² manufacturing facility.
Introduction of Virtual and Digital Consultations
Combilift is well known for its free design and layout services it offers customers as a way to resolve problems and allow for the maximised use of available space.
Previously conducted on-site by technical staff, these consultations have been migrated to a virtual and digital platform, using video communication applications such as Whatsapp customers are now able to take Combilfit technical staff on on virtual tours of spaces and provide photos giving them a good overview of requirements and any potential problems.
The adoption of digital technology has allowed Combilift to still offer its free design and layout services in a safe manner and allow them to provide 3D designs to customers with minimal delays.
Management Communication
Combilift management is continually providing updates to employees via video updates which have temporarily replaced staff assemblies that used to occur on a regular basis.
Martin McVicar CEO and Co-Founder of Combilift believes that:
“The on-going communication ensures employees are continually informed and therefore understand that the measures we are taking are in everyone’s best interests.”
This weeks blog has provided an overview of the comprehensive health and safety measures Combilift Ireland has implemented in response to Covid-19, to allow their manufacturing operations to continue delivering industry leading materials handling solutions to their customers.