9 Common Forklift Hazards
Forklifts are large and heavy pieces of machinery, due to their size operating them in an inappropriate manner or without due care can make them hazardous to operators, pedestrians and facilities.
In this week’s post we briefly describe ten common forklift hazards and how they can be mitigated to improve safety.
1. Improper Operation and Use
Operating a forklift improperly via actions such as speeding, racing or sharp cornering is a serious hazard to operators, loads and the forklift itself.
Operating in the manner above greatly increases the chances of accidents such as collisions or unit tip overs occurring that can result in injuries, fatalities, product and equipment damage.
Forklifts should only be operated for the purpose they’re designed and engineered to complete the safe lifting and maneuvering of palletised and heavy goods.
Trying to use the forklift for unintended purposes similar to inappropriate operation greatly increase the chances of accidents occurring.
Ensuring all forklift operators hold a valid forklift licence and have completed up to date training is likely to decrease the likelihood of rogue operators utilising the forklift inappropriately, as they possess the required driving skills and are aware of their obligations when operating the unit.
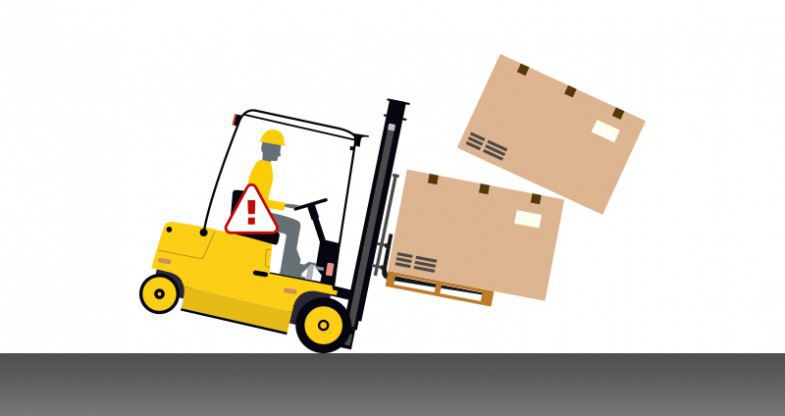
2. Load Hazards
Every forklift is rated by the manufacturer to be able to safely lift a maximum load limit.
Overloading the forklift above its maximum safe load limit is a serious hazard overweight load will decrease its stability when the load is lifted by the tynes, heightening the likelihood that the load will fall and the forklift may tip over endangering the operator and potentially damaging the load and forklift.
Further increasing the potential for accidents to occur from unit overloading are unsecured loads, without proper restraint were the load to fall off the tynes or the forklift to tip over the load and can cause serious injury or damage.
To overcome instances of forklift overloading it is imperative that all operators are aware of the units maximum safe load limit via its rating plate.
All load weights should be known before lifting commences and loads shouldn’t be lifted until it is confirmed that the load is within the units load limit.
All loads should be secured before they’re lifted to ensure it can’t move unexpectedly.
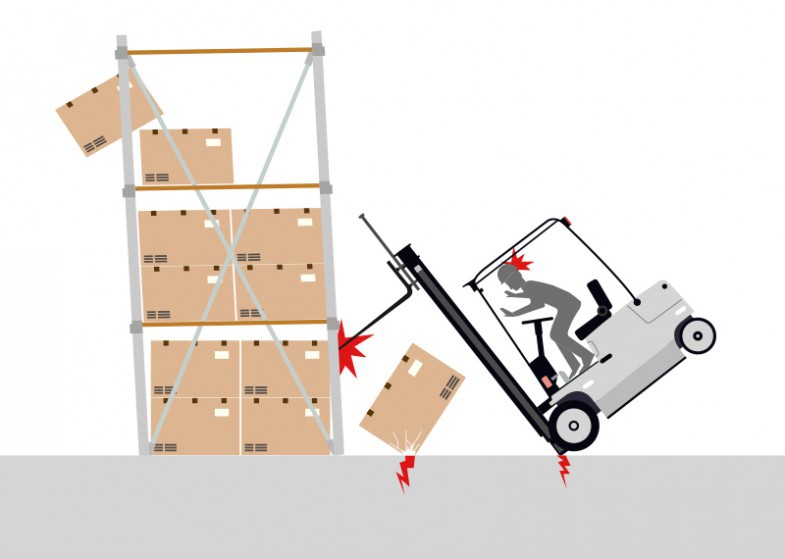
3. Insufficient or Incorrect Maintenance
Not properly maintaining a forklift can increase the risk of an accident occurring.
Broken lights, alarms that don’t work, worn tynes, damaged chains and fluid leaks are examples of problems that can occur if a forklift isn’t properly maintained.
It is imperative from a safety aspect that any forklift with problems such as those mentioned above are tagged out and not used until everything has been repaired.
Setting up forklifts on scheduled maintenance plans are the best way to ensure units are regularly inspected and maintained to keep them in optimum operating order.
4. Pedestrians
Non-essential pedestrians working in the same area as forklifts are a major hazard as they can be seriously injured if they were to be struck by the unit.
Having a clearly defined traffic management plan for areas where forklifts and pedestrians work in close proximity is imperative to increase pedestrian safety.
Additionally installing safety measures such as guard rails and line markings to separate machines and pedestrians at intersections, as well as installing spot lights and horns on forklifts to alert pedestrians to the unit’s presence are essential to mitigate pedestrian hazards.
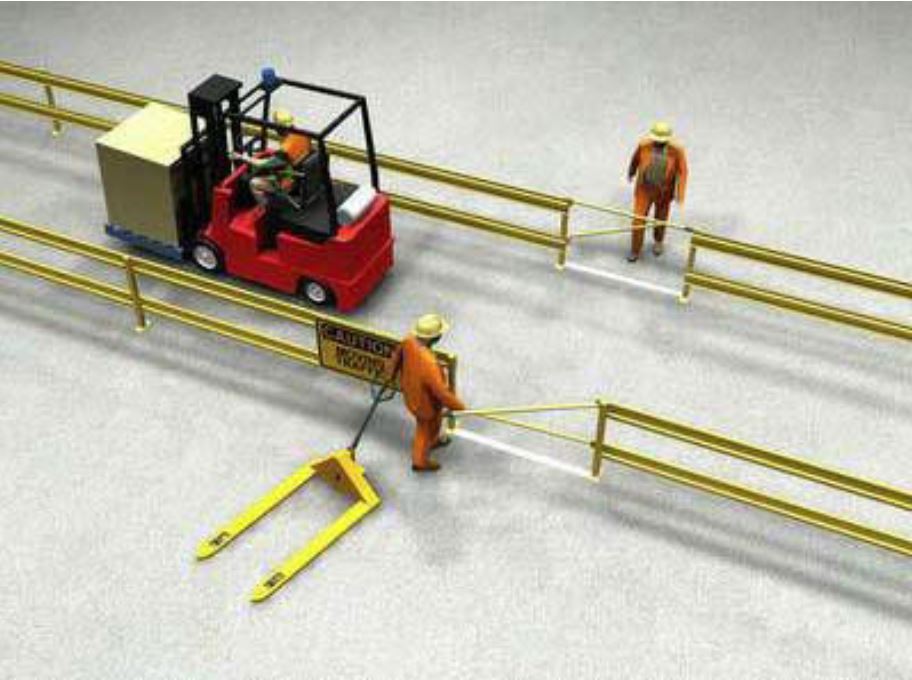
5. Floor Conditions
The condition of the floor of the forklift working area can present a number of hazards including debris, puddles, unstable ground and floor obstructions.
Wet and slippery floors can cause a forklift to skid, whilst cracks and pot holes in the ground can cause the unit to tip over.
Any wet and slippery hazards should be cleaned up, debris and obstructions removed and cracks and pot holes should be fixed to ensure a safe work environment for forklifts to operate over.
6. Overhead Obstructions
Overhead obstructions such as mezzanine levels and low hanging doorways present another potential hazard for forklifts.
If a load is being transported with the tynes raised to high a collision with the obstruction may occur that may cause damage to the load, forklift or the overhead obstruction.
To best mitigate the potential for overhead collisions it is imperative all loads are transported with the forklifts tynes lowered with only a short height above the ground.
Operators should also be aware of the forklifts overall lowered height via its rating plate, whilst labelling the clearance levels of mezzanine levels and doorways can assist operators in maneuvering their forklift and load safely under overhead obstructions.
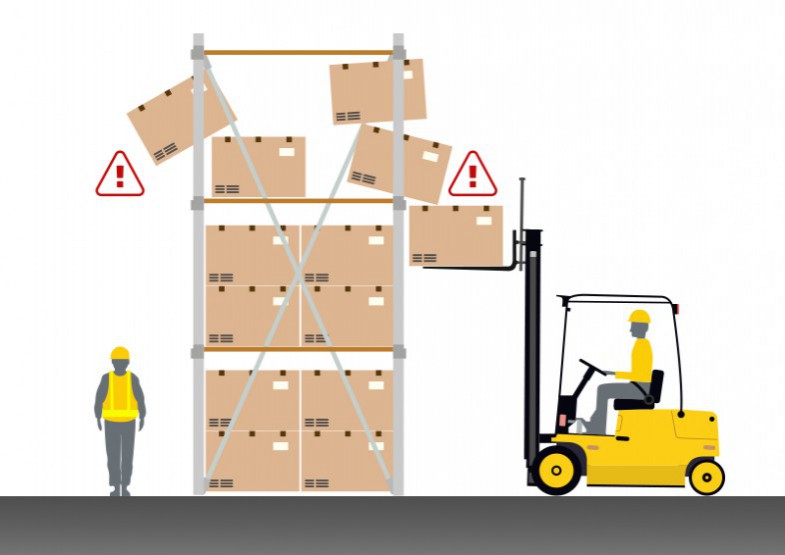
7. Unit Refueling
Refueling and recharging a forklift pose potential safety hazards due to the combustibility risk of LPG and diesel fuels.
Recharging batteries can also present a combustibility risk due to the gases generated whilst also presenting an electrocution risk if wet or wires are exposed.
To best mitigate the hazards of refueling a forklift designated refueling areas should be built solely for the purposes of refueling in a safe controlled environment.
Potential sources of ignition such as cigarettes or tools that spark should be kept well away from refueling areas.
Refueling areas should be built with high levels of ventilation to allow toxic fumes to dissipate efficiently reducing the potential for fire to occur.
8. Attachments
Forklift attachment are another source of hazards as their installation directly affects the units lift operating clearances and safe lifting capacity.
All forklift operators should be trained in the correct use of all attachments they must operate including relevant safety protocols and revised safe capacity and lift limits.
Poorly maintained attachments can also pose a safety risk, worn out tynes, stretched chains or other damaged parts of the attachment can put the operator at increased risk.
Before operating all attachments operators should visually and mechanically inspect them to ensure they function correctly and are safe to use.
Any attachment that is malfunctioning should be immediately removed from service and repaired or replaced before being utilised again.
It is also imperative that all attachments are compatible with the forklift and can be safely installed on the unit.
An improperly installed attachment when fully loaded can cause severe injury and damage were a malfunction to occur.
9. Blind Spots
Forklift blind spots are dangerous when operating a forklift since unexpected impacts can cause serious injuries.
When fully loaded an operators view is obstructed.
Similar to load obstruction poor visibility from poor lighting or weather conditions such as rain can make it harder for forklift operators to see.
To decrease the risk of collisions pedestrians need to be directed away from walking or working in a forklifts blind spots.
Driving routes should be planned to best avoid blind spots, obstacles and other hazards when transporting large loads, whilst spotters should be employed when maneuvering around blind spots.
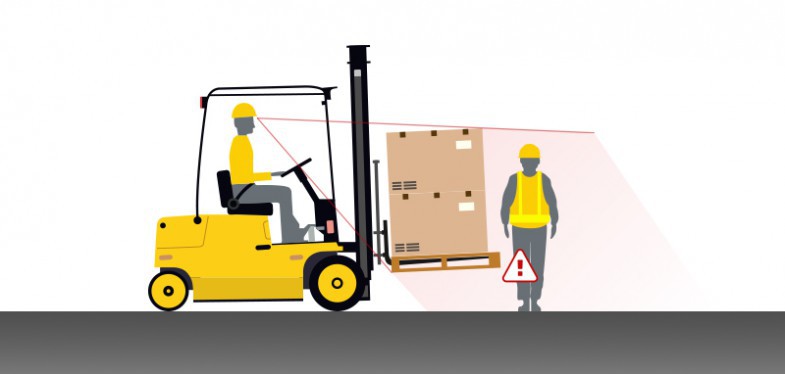
This week’s post has highlighted nine common forklift hazards and ways they can be mitigated.
For further information on how to mitigate the risks of forklifts hazards contact us on 13 22 54 or complete a contact form and we will respond.